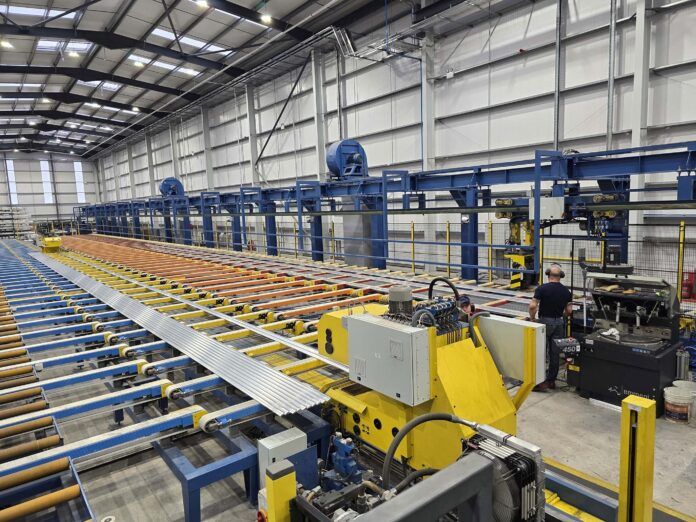
Powder coating continues to be the first choice for architects when choosing finishes for windows and facades. With its limitless colour choice of coatings, metallic finishes, sublimation finishes, such as wood and stone appearances and special patina replications, it is clear why the aluminium finish is so popular.
As with any material finish, preparation of the substrate and quality of coating is crucial to offering a sustainable finish that will last a lifetime, something that QUALICOAT licensed applicators uphold in their Specification.
Various country Members of the global specification, QUALICOAT, have undertaken extensive work over the decades to further refine the products and processes to ensure finishes continue to offer enhanced sustainability. The latest development in this ongoing work has culminated in the new QUALICOAT 3.0 specification.
Introduced just two years ago, the first project to be certified in QUALICOAT 3.0 in the UK and Ireland is the Hurlingham Waterfront project on the River Thames for Hamilton Architects. The project consists of a substantial amount of aluminium Brise Soleil which is being installed over the next few months by Eire Facades UK Ltd. The aluminium extrusion and finishing has been completed by AMS of Cork, who have been awarded the QUALICOAT 3.0 certificate as part of their continuous improvement drive.
Pat O’Hara of AMS takes up the story “As standard with all our façade systems, we have extruded the fins that make up the shading and privacy screens using an alloy made from Hydro low-carbon aluminium with a 50% post-consumer scrap and a guaranteed footprint of just 3.0kg CO2 per kilo of aluminium.
“QUALICOAT 3.0 requires that alloys fall within the EN573-3:2019 Standard, which can be met using primary or secondary (recycled) aluminium and requires the following three tests to be carried out by an independent testing authority, Optical Emission Spectroscopy (OES), Anodic Cyclic Polarisation (ACP) and a Metallographic Study for Aluminium.
“QUALICOAT 3.0 has been developed to ensure that the aluminium alloy does not become a contributing factor to any premature failure of a powder coated finish. By ensuring that the alloy is of the correct standard, with reduced inclusions and improved grain consistency, it has been demonstrated by QUALICOAT that architectural powder coating can be further enhanced for sustainability, especially when used with Class 2 powders, which is the case in this instance.
“Certificate number 5 means we are just the fifth company in Europe to have applied for and reached this standard, and being both an extruder and powder coater means we are in total control of the quality of metal we powder coat on one of our three lines in Cork daily.”
The up-to-date QUALICOAT Specification, which includes QUALICOAT 3.0, is freely available for download via the UK & Ireland Association website, qualicoatuki.org.
The website also offers an up-to-date list of licensed UK and Ireland Powder Suppliers, Pretreatment Suppliers and Applicators including the applicators who carry the Seaside class accreditation.