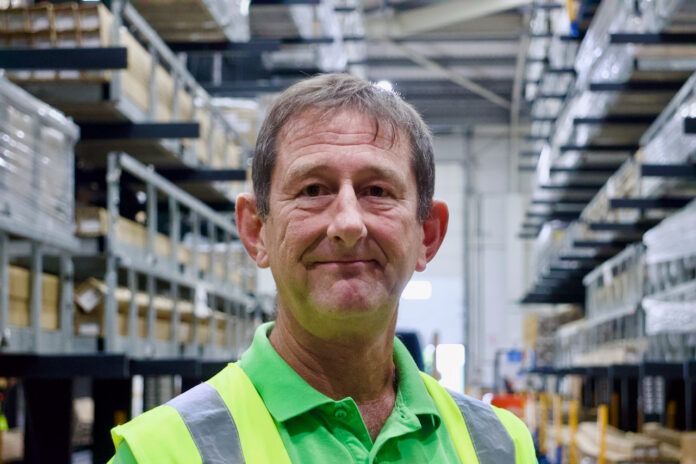
Thermoflex is now the best-performing flexible silicone rubber spacer bar in the world, according to test results from IFT Rosenheim and approved by BFRC in the UK.
Following years of development, and ratified by Europe’s leading accreditation body, Thermoflex from Thermoseal Group now boasts a thermal conductivity of 0.125W/(mK) for the UK’s preferred thickness of 4.8mm.
This means Thermoflex cannot be substituted with any other foam spacer system without putting the whole window through a recalculation. Failure to do so will result in a non-compliant window.
Thermoflex, on the other hand, can substitute other flexible silicone rubber spacer bars without recalculation.
“It is official – Thermoflex warm edge spacer bar is the best performing flexible premium silicone foam rubber spacer in the world,” Thermoseal Group’s Sales Director Mark Hickox said. “Thanks to 15 years of research and development right here in the UK, we have developed a premium product, as standard, which outperforms other similar products.
“One reason for this is that we make Thermoflex in the UK with 100% silicone, compounded by us at our impressive modern facility in Wigan. Other competitor products in the UK – which claim to be as good as ours – are generally a compounded blend containing EPDM rubber, which is a cheaper raw material than silicone, and is less thermally efficient.”
The new 0.125W/(mK) value achieved by Thermoflex is a massive improvement on the previous conductivity value of 0.175W/(mK), and puts the spacer bar into a thermal efficiency league of its own.
“A 0.05W/(mK) improvement may not sound a lot when you are comparing conductivity values as low as these, but when regulations, specifiers and building owners are demanding increasingly thermally efficient windows and doors, advances like this are absolutely crucial and help our customers remain competitive,” Mark said.
“There are also tangible gains to be had from this improvement. For example, Document Q of the Building Regulations requires laminate glass in certain windows for security reasons, which lowers the overall U-value of the window. So, while a normal window would get you a Window Energy Rating of an A, the introduction of laminate glass could make this drop to a B. If you were to use Thermoflex, you would generally achieve a WER of an A in both cases.”
With the possible requirement for bespoke U-values for each individually manufactured window, following the introduction of the Future Homes Standard in 2025, the thermal performance of each component part is expected to be critical.
“By moving away from a ‘standard’ window when calculating U-values, window fabricators will have to produce a certificate for every window manufactured to prove that it complies with the revised regulations,” Mark said. “And the fact that Thermoflex is higher performing than other similar spacer systems could easily make the difference between a window complying or failing.”
Thermoseal Group manufactures Thermoflex at its site in Wigan using the very latest compounding, extruding and processing machinery.
Thermoflex is also extensively tested alongside other components supplied by Thermoseal Group – such as desiccant, sealant and injection moulded fittings – to ensure that the insulated units exceed the expected lifespan of the windows they are used in.