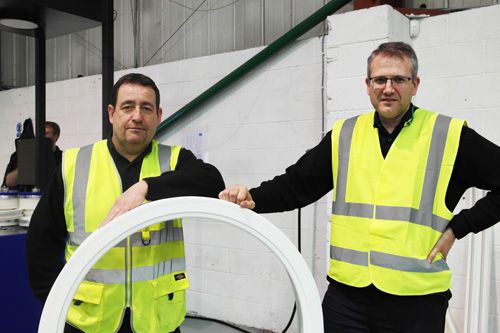
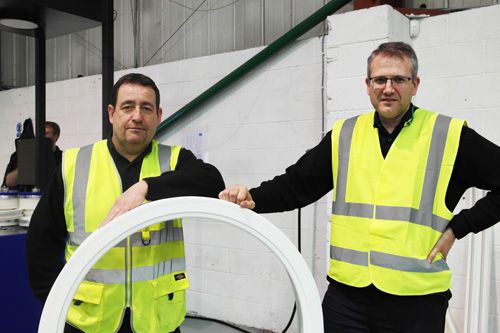
Quickslide is now offering a superior finish as well as faster turnaround on curved and arched frames, with a EUR 60,000 investment in a new state-of-the-art in-house bending facility.
The fabricator’s choice of the TIM-ING bending centre means the action is not only faster – as little as 10 minutes per curve – but also a cooler working temperature makes it far more energy efficient, and its ‘sophisticated’ automation and use of multiple 3D cameras is said to give ‘near perfect’, consistent results with ‘practically zero’ waste.
Operations director, Ben Weber, says the move is in keeping with Quickslide’s philosophy to take complete control of as many manufacturing processes as possible.
“We already have our own in-house foiling and painting facilities as well as PVC-U and aluminium fabrication,” he said. “This is a big step forward for us as VS’ are notoriously difficult to work with when it comes to bending profiles, so now to be able to offer consistent and reliable quality in a fraction of the manufacture time gives us another USP within our market place.
“As well as a single point of answerability for quality control and no buying-in costs, the TIM-ING is also a highly advanced system, using much less heat on the profile, so there is no surface damage to colours or woodgrains and an all-round better and more consistent product quality.”
Sales & marketing director, Tom Swallow, added: “Quick turnaround and consistent quality on arched products is what the industry has been in dire need of since I can remember. It is a fantastic opportunity for Quickslide to now be able to offer this service to our trade partners and give them the edge against their competition.”