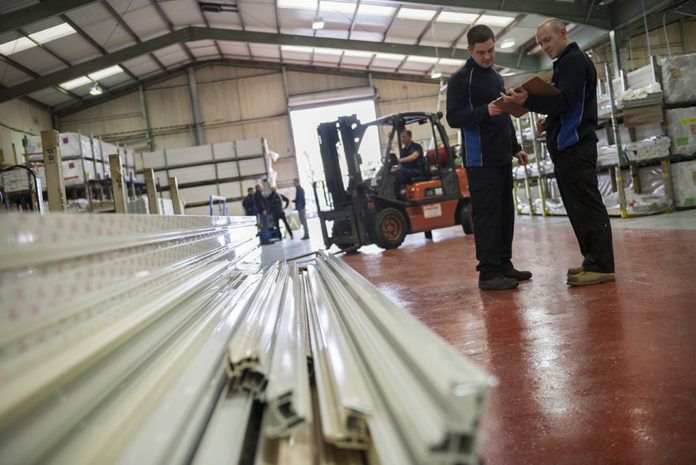
West Yorkshire based fabricator, Quickslide, has announced that it has rolled out double shift patterns throughout its factories, a move that is designed to further improve its service offering, as well as ensure it is best placed to cater for a significant upturn in sales orders for all its market leading products.
Quickslide, which manufactures a complete range of PVC-U and aluminium windows and doors, first introduced a double shift working pattern in January 2019 due to high demand for its heritage style vertical sliders. The company reports that this has proved to be highly successful and has enabled it to further enhance its service to trade partners by offering improved lead times, even during particularly busy periods.
And now that the increased vertical slider production has proven to be so beneficial, Quickslide has expanded the option of double shift patterns to both its aluminium and PVC-U casement facilities, giving the company the ability to uplift capacity – factory wide – as and when it is required.
Tom Swallow, sales and marketing director, commented: “With a double shift pattern operating in our vertical slider facility, we were able to offer a low cost three-day express lead time on a selection of our VS products even during our busy summer months. This allowed us not only to sustain a competitive advantage within the wider industry, but also means that we are now well prepared for periods of high-volume output later in the year as well.
“By extending the option of double shifts to our other factories, we are now also very well positioned to respond to the demand for our aluminium offering, which has been bolstered by the ongoing upturn in popularity for aluminium products. Furthermore, should the need arise, we can now significantly increase the output of our new range of Deceuninck PVC-U products that were introduced earlier this year, and which include the 2800 Storm Sash casement windows and doors, Slider 24+ sliding patio doors and G-Award winning Heritage flush sash windows and doors.”