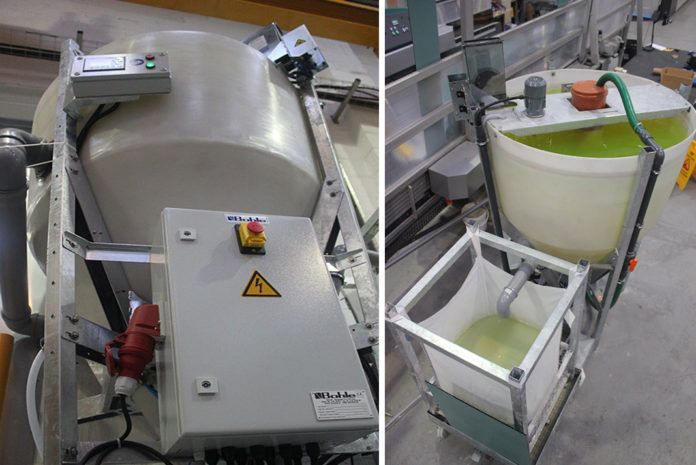
Glass processors have only months to ‘tap’ into EU funded grants to improve the management of their waste water, according to Bohle.
With the UK teetering on the brink of a hard Brexit, the glass consumables, machinery and hardware specialist has warned that EU funding streams are about to run dry.
It warns this could mean that glass processors miss out on the opportunity to access grants to fund up to 50% of the purchase cost of coolant and cleaning management systems, lowering their operating costs, improving edge quality and reducing the environmental impact of their operations.
Dave Broxton, managing director of Bohle, said: “EU grants of up to 50% of purchase costs are currently available to fund improvements to manufacturing processes, which deliver efficiencies, and which reduce waste, including waste water.
“With the high levels of usage of water as coolant in glass processing there is a major opportunity to improve product quality, lower your operating costs, while also reducing your environmental impact by improving the way that you manage coolant.”
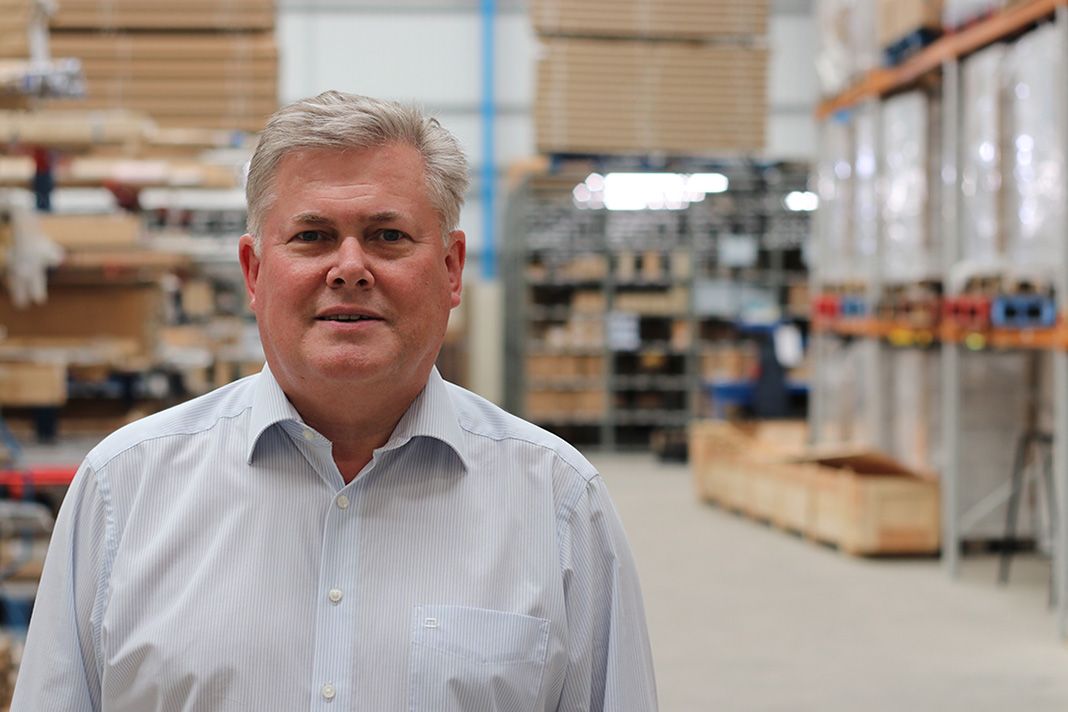
According to Bohle, clean water, especially with added coolant, increases the performance of machinery by up to 20% and the service life of tools by up to 30% – but it can all too easily become contaminated with particles from drilling, polishing and grinding.
This carries a potentially far higher price tag in lost man hours, falling product quality, in addition to reduced service life of equipment, says Bohle.
The cost of keeping coolant clean can also quickly add up. Modelling by Bohle reveals that using just 400 litres of water as part of your weekly cleaning cycle equates to a yearly water consumption of approx. 20,000 litres as well as high cost for its disposal.
Suitable for a wide assortment of grinding, drilling and sawing glass equipment, Bohle sedimentors use a sophisticated and automated, multi-stage process to remove contaminants from coolants and water. This includes filtering of glass particles of < 5 µm or less but doing so using far less energy.
Combined with improved product quality and increased service life as well as trimming around 10 per cent off the costs of water disposal, it suggests sedimentors will pay back against purchase costs in as little as a year.
“This is on the assumption that you’re funding the purchase in its entirety yourself. If you can secure grant funding for half of the cost, a sedimentor could pay for itself in as little as six months,” Dave added.
Under the EU funding scheme, businesses can apply for a 50% contribution towards projects with a maximum capital cost of £25,000 (maximum £12,500 grant). This is accessed through the Growth Hub network and Local Enterprise Partnerships.
“You have a choice,” continued Dave. “There is growing pressure on the glass processing industry to manage waste water more efficiently and sustainably. This includes potentially significant penalties for polluters and exclusion from opportunities for failure to meet sustainability criteria set by prospective customers.
“Alternatively, you can access funding for up to half of the cost of a sedimentor, improve your edge quality, extend the life of your tooling and make your business more sustainable.
“If any of this sparks your interest, get in touch with us now and we can work with you to specify the right option for your business and support you through the application process.”