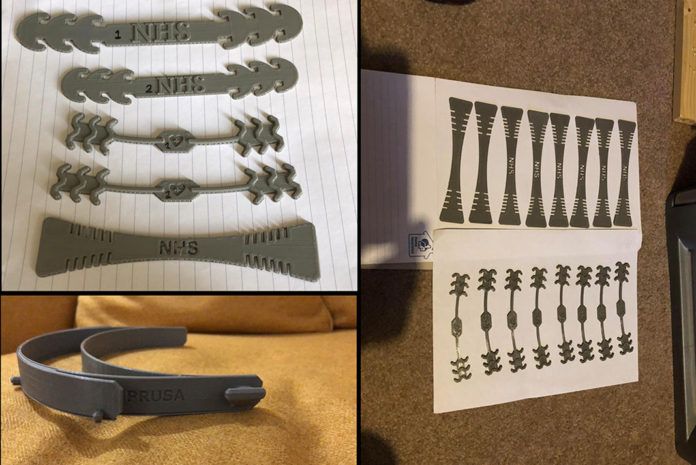
Epwin Window Systems is using its 3D printing capabilities to produce two types of Personal Protective Equipment (PPE) to support NHS frontline workers.
Clare O’Hara, managing director at Epwin Window Systems, said: “NHS staff are doing an amazing job and we all owe them so much. Two members of our Epwin team, systems developer Alan Humphries, and engineering service manager Steve Coxill, saw how they could use our equipment to give something back.”
Working in line with social distancing advice, Alan and Steve are producing two types of PPE. The first is ‘ear savers’, which are worn behind the head with face masks to stop the elastic rubbing the wearer’s ears. These are being distributed to healthcare settings near Epwin Window Systems’ headquarters in Telford, Shropshire. According to Epwin, feedback so far has been ‘exceptionally positive’.
Steve Coxill commented: “I heard from one wearer that she had used the ear savers on her last shift and she couldn’t explain how great it was. She said behind her ears were red raw and just using the device for one shift had freed her of so much pain and her ears can start to heal now. They are easy for her to sterilise and keep in her pocket without getting in the way till needed. It was amazing to hear we are able to do something to help.”
The second item is headbands and chin supports that make up face shields. This is reportedly being done as part of a much larger coordinated group, 3DCrowd UK. Ranging from hobbyists to professional 3D printers, 3DCrowd UK co-ordinates a community response, printing, collecting and distributing the face shield parts made by volunteers up and down the UK.
Steve commented: “Each set takes around three hours 15 minutes to print and there is a strict set of procedures to follow, such as wiping down the work area to sanitise, wearing disposable non-latex gloves to handle any parts and putting each batch into a ziplock bag, which is then dated to ensure it is enclosed for at least three days to avoid any contamination risks.”