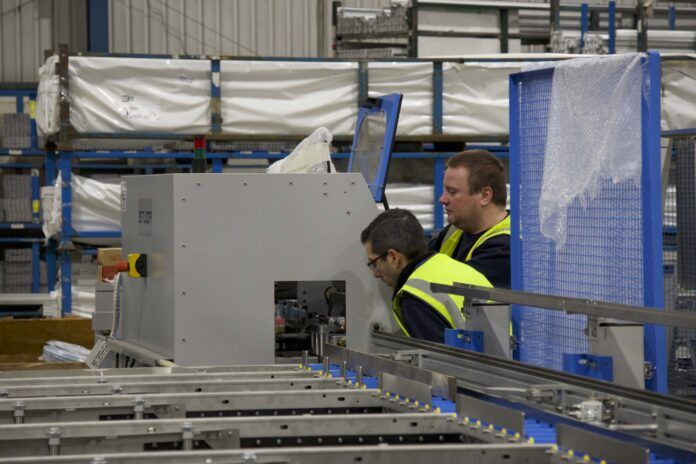
Emplas has continued its multi-million-pound investment in its state-of-the-art manufacturing facility with the addition of two new Stuga ZX5 automated sawing and machining centres.
Installed in its main manufacturing facility, the two next generation cutting and machining centres bring new precision to window and door manufacture, while also significantly increasing capacity.
This includes up to 800 windows each per week , building on the cutting and machining capability of Emplas’ pre-existing machining and sawing centres.
Installed in March as part of a major investment programme to deliver increased flexibility to its customers, Jody Vincent, Sales Director, Emplas, said the six-figure investment gave the fabricator one of the UK’s most advanced window and door manufacturing facilities.
“We have ambitious growth plans but we are committed to delivering them on the strength of product quality and the flexibility that we bring to service”, he said. “That starts with precision in preparation of the profile.
“The investment that we’re making with the addition of two new Stuga cutting and machining centres, builds additional foundation into our model, supporting growth, driving even higher levels of product quality, and allowing us to bring even more flexibility to our offer.”
Emplas’ two new Stuga ZX5s are built around an advanced rotary tooling ring with eight high speed spindles. This gives it a 360° machining capability, maximising output with ‘V’ and ‘Y’ notches produced on either side of the profile in a single pass.
Part of its continuing multi-million-pound investment programme and infrastructure investment strategy, the new Stuga sawing and machining centres build on the pre-existing capacity delivered by Emplas’ three Schirmer machining and cutting centres, and a pre-existing Stuga.
Emplas is currently reorganising its factory footprint, following the addition of a second 25,000sq ft manufacturing space, which will house its expanded composite door offer.
The release of space within its pre-existing 57,000sq ft facility will accommodate new machinery and further optimise production.
“It’s been an exceptionally busy start to the year but the changes that we’ve made provide a solid foundation for our long-term growth”, continued Jody.
“We’re committed to a programme of continuous development, investing in our teams, our digital infrastructure and our manufacturing facilities to bring ever better product quality and improved service to our customers”, he concluded.