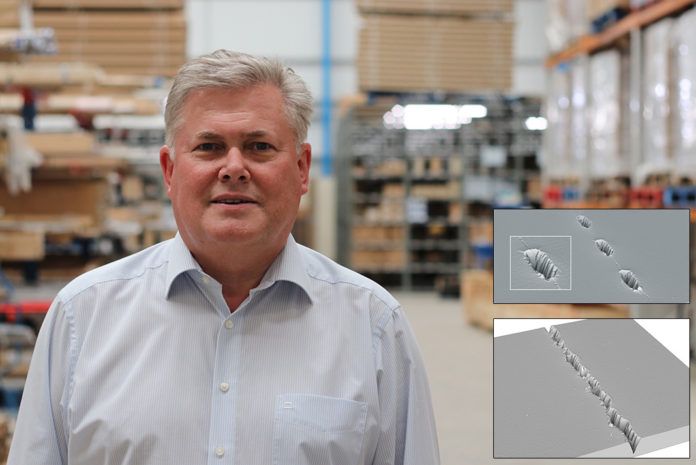
Bohle has warned the failure under thermal stress of centre panes in triple-glazed could cost the industry hundreds of thousands of pounds.
While the uptake of triple-glazing in the UK may have lagged behind expectations, the glass consumables and hardware specialist, says with more triple-glazed units fitted in the UK, the risk of centre-pane failure under thermal stress is continuously increasing.
This has prompted an EU funded study, which includes specific focus on edge-quality and how the glass is cut as a cause of failure, drawing on contributions and expert testimony from Bohle.
“The use of low e on face 3 of the unit as part of its thermal make-up, can lead the middle pane in a triple-glazed unit to heat up far more than it would do in a standard double-glazed unit,” said Dave Broxton, managing director of Bohle.
“This increases the pressure on the glass. In larger units this is less of a problem as the glass can flex and the pressure can be absorbed.
“Within smaller units with shorter edges, the glass is, however, essentially too stiff to bow out and it can lead to stress cracking of the centre pane or failure of edge-seals.
“The study is consequently focussed on the importance of edge-quality in defining the structural integrity of the glass – and its ability to withstand thermal stress.”
As the defining factor in edge quality, the research team has drawn down on Bohle’s expertise in cutting wheel technology. This includes long standing developmental partnerships with Brembana, Grenzebach, Hegla, Intermac, Macotec and Lisec, to help them optimise performance of industrial glass cutting lines.
“When you score glass with a cutting wheel you effectively transmit tension into it. This creates a ‘fault line’ in the glass, which as you bend it, triggers a break along that line,” continued Dave.
“How clean that break is – and how stable that glass is going to be, either in the furnace or in a triple-glazed unit – is defined by multiple factors including the individual characteristics of the glass; the shape of the cut; the diameter of the cutting wheel; the angle of the cut; cutting force; cutting speed; and the cutting fluid used.
“Get one of those elements wrong and you increase the chances that your triple-glazed unit is going to fail under thermal stress.”
Bohle supplies an extensive range of tungsten carbide and PCD (polycrystalline diamond) cutting wheels and their holders, sold under its Silberschnitt brand. This includes CutMaster Gold. A highly engineered tungsten carbide cutting wheel, it is said to be ideally suited to cutting of float line and laminated glass, with a service life of eight to 10 times longer than a standard cutting wheel. Most importantly, adds Bohle, it maintains a consistently high cutting quality from the first to the last cut.
With the study due to report later this year, the study again highlights the importance of edge quality in IGU manufacture.
“Edge and finish quality can deteriorate very quickly if the right cutting wheels aren’t used, or just as importantly, the cutting edge of the wheel deteriorates over time,” Dave said.
“Our focus is on the development of products, which improve quality and reduce wastage, in production but which also improve edge quality and which guard against potential costs down the line,” he concluded