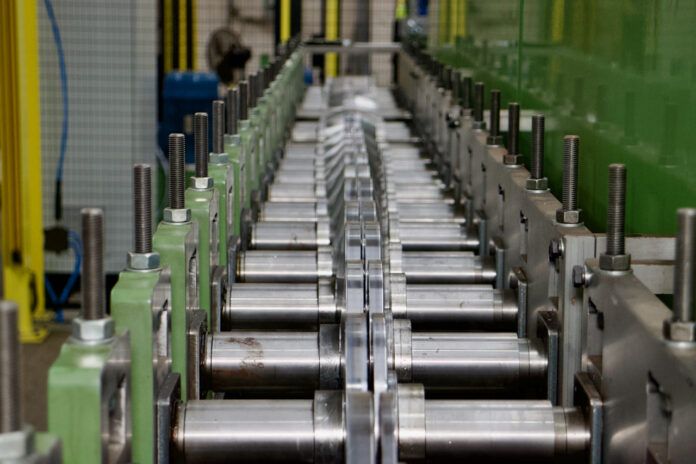
Steel reinforcement and profile roll-forming specialist Anglo has invested more than £1 million in the UK’s most advanced roll-forming line.
Delivered as part of a multi-million-pound investment programme, the new double-sided CNC line features 24 passes, making more and smaller adjustments to profile angles in manufacture, reducing stress on the steel, and improving product quality.
Introducing increased precision in manufacture, it has given Anglo the opportunity to manufacture far more complex profile shapes. Double-sided, it also allows Anglo to significantly reduce tool change time, increasing efficiencies and lowering costs – savings that managing director David Evans said Anglo was passing on directly to its customers.
“It’s the best in British manufacturing technology,” he explained. “What’s unique about it is that it’s a double-sided production line, which means that we no longer have tooling downtime. As we’re tooling one part of the machine, the other side can be running. And when that side is completed, we can then be rolling on the other side of the machine within about 10 minutes.”
The line also rolls directly from the coil, punching and cutting ‘on-the-fly as part of a continuous process, delivering significant efficiency gains, while CNC control, brings increased precision to manufacture.
Operating from a two-acre site in Newton Heath, Manchester, Anglo was founded in 1989 as a specialist supplier of rolled steel reinforcements. Since it has supplied more than 250 million metres of steel reinforcement – enough to stretch around the equator more than six times. This includes its cut-to-size service, which eliminates the complexity and labour required to handle full bar lengths, while also significantly reducing waste.
Putting a deal in place with leading venture capitalists Octopus to fund growth in 2015, the company has gone through a major restructure, ending in acquisition by the Amari Metals Engineering Group in 2021, acquisition triggering another multi-million phase of investment.
“The new line isn’t the end of our journey, we will bring increased automation into our manufacturing process, with plans in place for another seven-figure investment in another line shortly”, David explained. “What the current new line gives us is consistency from batch to batch so we can be certain that every section we’re rolling is perfect. There’s very little variation and very little setup time, delivering efficiency gains which we pass directly onto the customer.”