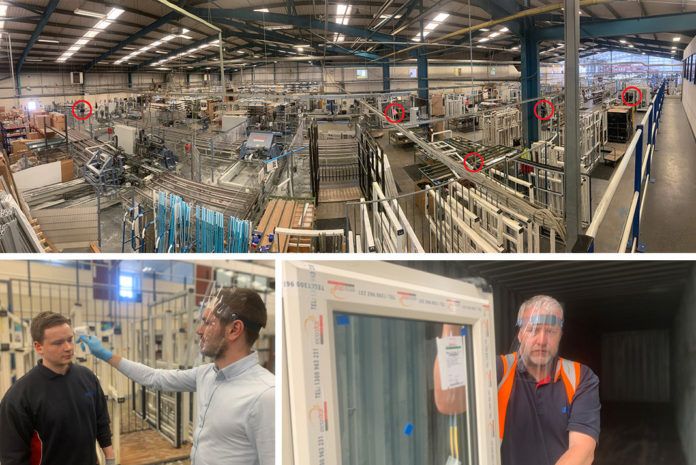
Emplas has highlighted its strategy to protect employees and customers after beginning a phased return to work with effect from 20 April, in a roundtable discussion hosted on Zoom. View an edited version of the discussion that also included Thom Emerson, sales & marketing director Ideal Window Solutions, Peter Wheeler, MD of SEHBAC and members of the glazing industry trade press at the end of this article.
Ryan Johnson, managing director, Emplas, said demand from the commercial sector, combined with that from its Australian retail business, Ecostar, which has remained open throughout the global pandemic, made getting back to work imperative.
“The demand for us didn’t ever stop,” he said. “The day after we shutdown we had calls from leading commercial contractors and housebuilders, asking us what our plans were to get back.
“That and the continuing demand from our Australian business, got us thinking about the return to work very early on.
“We’ve not just ‘come back’, we’ve been planning the safe and phased restart of our operations for weeks – and I believe that that’s something which will benefit us and our customers going forward.”
This includes major investment in PPE, new signage, hand sanitiser cleansing stations, a restructure of its factory floor and offices, as well as the introduction of new deep cleaning schedules. All employees are also subject to daily temperature checks.
Emplas’ focus, has, however, been as much on driving a new culture of awareness amongst employees as to how to stay safe at work in the ‘Covid-era’.
This includes a dedicated training programme and assessment, which all employees must take and pass, before being allowed back to work. This includes developing an understanding of how COVID-19 spreads, its symptoms, and how to mitigate the risk of catching it through the use of PPE, social distancing and hand and respiratory hygiene.
Ryan continued: “We’ve come back initially with 12 fabricators. That’s 12 people in an 80,000ft2 factory. Each and every person on site has also gone through a full training and assessment before being allowed to start work.
“They have manufactured 275 windows in our first week back. It’s a fraction of what we normally produce but it’s not about volume at this point – it’s about safety. Starting now – and phasing our return – gives us control, the ability to check and refine our processes, and to make sure that we are doing everything we can to minimise risk to our people and our customers.”
Emplas has also launched a series of guides to support installers in getting back to work based on its direct experience of retail through T&K Home Improvements and Ecostar – both of which are already at work suppling customers.
This includes the launch of a new retail support guide, which offers installers advice on how to adapt their offers, win business and guidelines for working; plus, safe operating procedures.
Designed to be sent out to homeowners the over-printable guide sets out new guidance for working in the home safely.
“It’s been transformative,” Ryan said. “We had had push-back from homeowners but once we set out new procedures and processes for safe working, the market has completely opened up.”
Social restrictions in some form are expected to stay in place in the UK until the end of the year. On 22 April, the Government’s chief medical advisor, Chris Whitty, said it was ‘wholly unrealistic’ to expect life to suddenly return to ‘normal’. The Department of Business Energy & Industrial Strategy (BEIS) stated: “There is currently no distinction between essential and inessential construction work in England. The Government’s position is that construction work can continue, provided the worker is not displaying symptoms of Covid19 (coronavirus), does not need to self-isolate for another reason, and that the work can be done in a manner consistent with the guidelines published by Public Health England (PHE).”
“We can’t ‘sit-out the storm’,” said Ryan. “COVID-19 isn’t like that. It’s going to be with us for some time. So, we need to adapt the way that we work, so that we can get back to some sort of new normality as soon as possible.
“That means putting in place new processes, new equipment – but above all, building understanding – so that we can get back to work safely. We’re on that journey and we’re putting in place measures and guidance to support our customers in doing the same, where they aren’t already doing so”, he concluded.