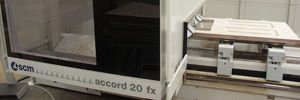
SCM Group UK reports that it has just received its seventh order for an SCM CNC machining centre from composite door manufacturer, Solidor, as well as an order for a Stefani Solution HD single-sided edge-bander with PUR gluing.
Having installed an SCM model Accord 20FX machine last November, alongside five SCM Record/Actionline CNC machines, Solidor realised it required even more machining capacity, as weekly production of 1,000 doors ‘was soon to become a reality’. As a result, Solidor’s operations director, Pierre Mifsud, called in SCM UK’s area sales manager, Ian McCarthy.
Pierre commented: “Production of our solid timber core doors is continually growing and we realised, last September, that we required even more capacity for 2014 just as the sixth CNC was being delivered and installed. So, we contacted Ian to take an order for another Accord 20FX for delivery in February 2014.”
The Accord 20FX is described as a ‘new generation’ modular machining centre, designed for machining operations requiring heavy-duty stock removal, along with high precision, providing ‘a top quality finish over the entire machining area’.
With a 3,680 x 1,380mm table to accommodate any size of door, there are six mobile aluminium bars, each fitted with vacuum suction cups which securely fix the door blanks to the table for subsequent machining via a vacuum pump. Rows of front and rear stops are said to enable the operator to easily position the door blanks on the table, assisted by two lifting supports that descend when the vacuum is activated and the machining cycle commences.
A powerful 8.5KW, 24,000RPM routing head, necessary for Solidor’s 48mm thick core construction, trims the outside of the door blank to the required dimensions and machines any face profiles or apertures for varying sizes and shapes for glazing cassettes.
After edge banding the four sides of the door, application of a thermo plastic skin to both sides of the door follows. Further machining is then carried out for various door locking systems, using an independent horizontal routing head with two outputs for the heavy-duty tools necessary for machining the lock and recesses. Machining for letter plates, handles, etc is carried out by the vertical routing head.
The Accord has a TR10 side tool magazine that accepts up to 10 tools to enable fast changing of the vertical routing tools. With the latest ‘Pro-Space’ safety system fitted, the Accord does not require safety mats or light cells, so the operator is able to remove trim off-cuts and aperture waste material during the machining cycle, thus saving valuable production time.
All of the machine’s pneumatic and electronic equipment is located in the Accord’s base, saving valuable floor space. The operator has the latest ‘Tecpad’ mobile control console, enabling full control of the Accord while the operator can view all the machining operations through the front safety guard window.