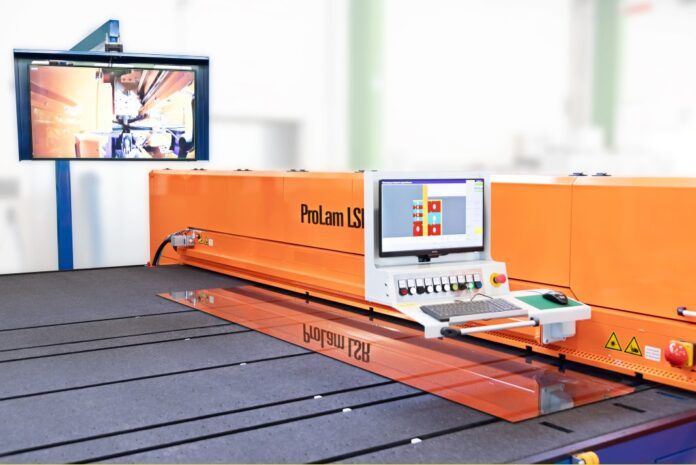
A new LSG cutting process that is part of the standard equipment of the ProLam LSR is 20% faster and has a laser diode heating system as its centrepiece, according to a representative of the flat glass machinery business, Hegla. Added value is generated thanks to the properties of the laser, they added.
“The thermal energy is bundled, focussed on the scoring contour and applied precisely to the film,” Helga’s representative continued. “Without the otherwise typical radiation losses, the transformation temperature is reached more quickly. During the heating process, the broken-out glass is pulled apart and then cut with a knife.
“The thicker the LSG, the greater the time advantages: thanks to focusing, the heat application is highly concentrated. In addition, the laser retains more of its strength when penetrating the glass than with conventional heaters.”
Bernhard Hötger, Hegla’s CEO, said: “The considerably lower heat loss to the surrounding pane and the air results in two more advantages that we did not expect to this extent when we first started developing the product. Even when thicker units are cut, the glass only becomes warm to the touch at the edges. The glass can move straight on to the next cut without waiting to cool down first.”
Bundling the thermal energy also has a positive effect on edge quality, Hegla’s representative explained. When the glass is pulled apart, only the heated film in the cut area is stretched. Tests by the Fraunhofer Institute have revealed that the remaining laminate remains unchanged by the local application of heat, reducing the previous causes of subsequent delamination to a minimum.
“LSR technology also improves the energy footprint,” they added. “The laser diode strip is divided in half and each side is partially or fully activated depending on the cutting length. The shorter duty cycle additionally reduces consumption.”