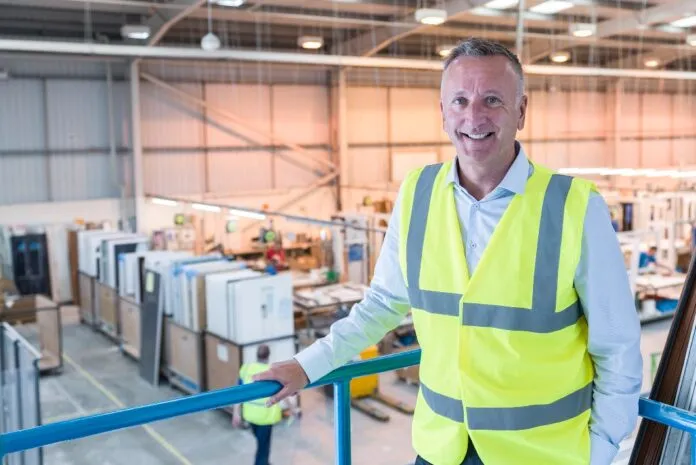
Leaders of Hurst Doors have built on the firm’s composite door manufacturing capacity by adding a new beam saw and two edge banders to the manufacturing facility.
Installed in the summer, the new beam saw moves bespoke door cutting to a dedicated process, freeing up capacity across Hurst’s three pre-existing CNCs as well as reducing wear and tear.
The two new automated edge banders further improve quality and support product development, the company’s representatives have said, for example the SFS Dynamic 2D-C hinge has been added to Hurst’s composite door ranges.
Kevin Wheatman, general manager of Hurst Doors, explained: “We currently cut all our composite doors, including our fire door range, down to size using the CNC as part of a single process in addition to machining window apertures, lock and hinge pockets. That generates a lot of aggressive dust which gets into the spindles and the bearings of the CNC. Over time, this has meant we’ve had to replace parts, losing time and capacity in the factory and increasing overheads.
“The introduction of the beam saw, to cut slabs to size, takes pressure off our CNCs and increases capacity but provides better quality.
“The edge-bander builds on that further, allowing us to improve our quality and finish, and provides a foundation for the evolution of our product offer, with the addition of the SFS easy-adjust Dynamic 2d-C hinge.”
Automation of composite door edging means that, in addition to standard white, edging will be offered in five different stock colours, plus any RAL colour on special order.
“Service and product quality on composites is key to our business and customers,” said Mark Atkinson, Hurst’s sales director. “The changes that Kevin and his team are making in the factory allow us to build both increased capacity into our composite door lines but also enhanced product quality.
“With new sales and marketing tools on the horizon, it’s a great time to switch to composite door supply from Hurst.” Read more about the business on the company website.