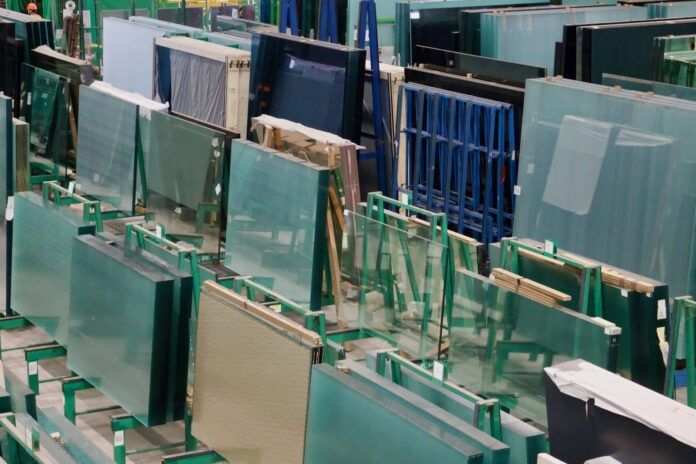
Cornwall Glass Manufacturing returned 1,437 tonnes of glass to Saint-Gobain Glass as part of its ‘Glass Forever’ scheme in 2023, which reflects the size and efficiency of its operations.
The recycled cullet dramatically reduced the raw materials used in the production of float glass, significantly reducing carbon emissions in the process.
“In a single year, we helped ease the burden on virgin materials to the tune of 1,724 tonnes, saving 1,006 tonnes of CO2 in the process,” Mark Mitchell, Cornwall Group’s chairman, said. “As a large glass product manufacturer, our contribution to Saint-Gobain’s Glass Forever scheme was always going to be significant, but interestingly that figure isn’t as high as it could be!
“We have invested in the very latest machinery and optimising software to ensure that we use as much of each sheet of glass that we buy, so less of it is returned as cullet and less energy is spent unnecessarily delivering it and collecting it.
“We also partner with the very best (UK-based where possible) glass manufacturers so that we only ever manufacturer quality products using quality raw materials. Again, this reduced the amount of waste glass being returned to Saint-Gobain Glass.”
The whole of the Cornwall Group – including Manufacturing, Mackenzies and Forward Glass – is on target to return 2,543 tonnes of cullet to Saint-Gobain Glass in 2024, saving 1,780 tonnes of CO2 and saving 3,051 tonnes of virgin raw material.
“A key advantage of operating as a group of companies is that we can create significant operational efficiencies that ultimately benefit our customers,” Mark said. “But these positive figures also demonstrate that those efficiencies translate into sustainability benefits, and we are pleased to be doing our bit in reducing our industry’s impact on the environment.”
Cornwall Group has invested in three new state-of-the-art Glaston Tempering Furnaces, representing more than £3m, with each going to different sites within the Group. Since they replace existing machines, they will each make a significant impact on the Group’s carbon footprint.
“A less than perfect furnace could result in sub-standard product, a bottle neck in our factories, or excess energy being wasted fuelling them,” Mark said. “These new machines are aligned perfectly with our vision for reduced waste and efficient manufacturing.”
Mark pointed out that those environmental wins are also valuable to customers.
“Large commercial contracts in particular are scrutinising the embedded carbon of all component parts,” he said. “So being able to demonstrate a sustainable supply of glass products could be the key to winning a place on the bigger projects, thus contributing positively to growing your buiness.”